Welding WPS: Usual Mistakes to Prevent and Just How to Correct Them
Welding WPS: Usual Mistakes to Prevent and Just How to Correct Them
Blog Article
Grasping Welding WPS Standards: Best Practices and Techniques for Top Quality Welds
In the world of welding, understanding Welding Procedure Spec (WPS) requirements is an important element that directly influences the top quality and stability of welds. Sticking to these requirements guarantees uniformity and reliability in welding end results. Nonetheless, achieving excellence in welds surpasses simply understanding the standards; it entails implementing best practices and techniques that boost the craft to a level of precision and skill that establishes apart the average from the remarkable. As we navigate with the complexities of welding WPS standards, uncovering key insights and techniques for achieving top-tier welds will be paramount for welders looking for to succeed in their craft and generate welds that stand the test of time.
Recognizing Welding WPS Criteria
Recognizing WPS requirements is vital for welders, designers, and inspectors associated with welding operations. By complying with WPS standards, welders can create welds that meet the needed mechanical residential or commercial properties and structural stability. Assessors count on WPS documentation to confirm that welding treatments are being complied with properly and that the resulting welds are of high top quality. Designers utilize WPS criteria to make welding treatments that make certain the sturdiness and reliability of welded structures.
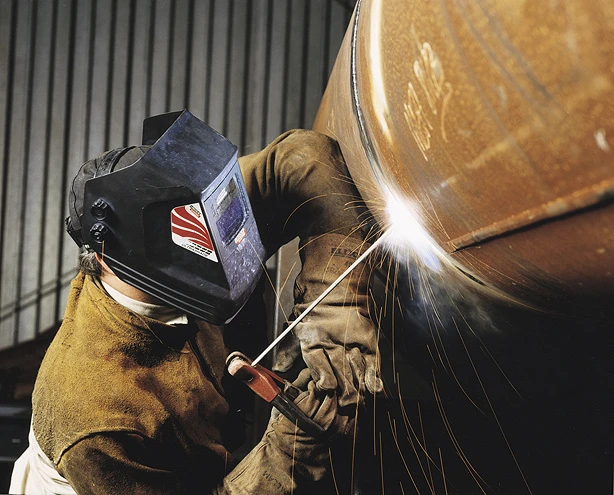

Vital Tools for Top Quality Welds
Grasping welding WPS criteria is important for welders to effectively use the important devices required for producing you can check here quality welds. The kind of welding maker needed depends on the welding procedure being made use of, such as MIG, TIG, or stick welding. Wire brushes and cracking hammers are important for cleaning up the weld joint before and after welding to eliminate any kind of impurities that might affect the top quality of the weld.
Key Methods for Welding Success
To achieve welding success, one should master the essential methods vital for creating high-quality welds. Preserving a constant hand and a stable welding position throughout the process is key to attaining precision and uniformity in the welds. By understanding these vital strategies, welders can elevate the high quality of their job and achieve welding success.
Ensuring Conformity With WPS Standards
Furthermore, preserving detailed documents of welding specifications, tools calibration, and evaluation outcomes is important for showing compliance with WPS standards. By diligently adhering to WPS requirements, welders can make certain that their work meets the needed high quality degrees and contributes to the general success of the welding task.
Troubleshooting Common Welding Issues
To resolve this, ensuring proper cleaning of the base metal before welding and making use of the appropriate shielding gas can significantly lower porosity. Additionally, distortion, cracking, and spatter are typical welding difficulties that can be mitigated through correct joint prep work, consistent heat control, and picking the appropriate welding consumables. By thoroughly understanding these common welding click for source issues and their root causes, welders can efficiently troubleshoot problems and achieve premium welds.
Verdict
In final thought, mastering welding WPS standards requires a thorough understanding of the guidelines, using vital tools, and executing vital strategies for effective welds. Ensuring conformity with WPS criteria is important for producing quality welds and preventing common welding issues. By complying with finest methods and methods, welders can attain consistent and reputable lead to their welding projects.
In the world of welding, mastering Welding Treatment Specification (WPS) criteria is a crucial component that straight affects the high quality and integrity of welds.When delving into the realm of welding techniques, a critical aspect to comprehend is the relevance and ins and outs of Welding Procedure Specification (WPS) requirements. WPS standards offer a detailed guideline for welding procedures, making certain consistency, top quality, and security in the welding procedure. The type of welding maker needed depends on the welding process being utilized, such as MIG, TIG, or stick welding.Achieving welding success with the proficiency of key techniques requires an extensive understanding and adherence to Welding Treatment Requirements (WPS) criteria.
Report this page